5 common quality problems in construction of self-drilling hollow bolt (SDA system)
Time:2024-07-30From:sinorock View:
Self-drilling hollow bolts are a crucial component in modern geotechnical engineering, widely utilized for both temporary and permanent support in rock and soil anchor systems. Their effectiveness in maintaining stability during construction and as part of the permanent support structure underscores the importance of ensuring high construction quality. Despite their advantages, several common quality problems can arise during the installation of self-drilling hollow bolts, compromising their performance and safety. This article explores these issues in detail and offers solutions to mitigate them, emphasizing the importance of adherence to industry standards and best practices.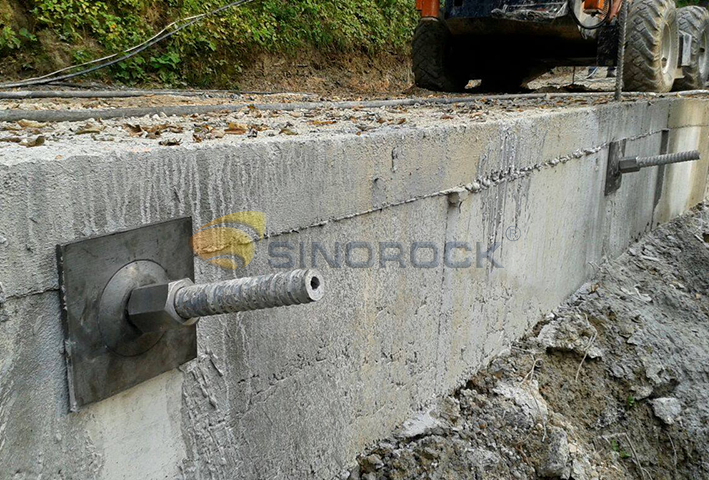
1. Incorrect Water-Cement Ratio and Insufficient Cement Dosage
Problem Description:
The water-cement ratio and cement dosage are critical factors in ensuring the strength and stability of the grouted self-drilling hollow bolt. An incorrect water-cement ratio or insufficient cement dosage can lead to weak grout, which may adversely affect the bolt's performance and the stability of the surrounding rock or soil.
Common Causes:
- Inadequate Cement Dosage: Sometimes, the amount of cement used may be less than required, leading to a grout mix that lacks the necessary strength.
- Uneven Mixing: Cement caking or poor mixing can result in inconsistent grout, affecting its ability to properly bond with the rock or soil.
- Measurement Errors: Field testers and supervisors may fail to measure the consistency of the cement slurry accurately.
Solutions:
- Regular Monitoring: Implement a rigorous monitoring process where field testers regularly check the consistency of the cement slurry. Ensure that it falls within the designed range before grouting.
- Proper Mixing: Use calibrated mixing equipment to ensure even mixing of cement and water. Address any issues related to cement caking immediately.
- Quality Control: Establish a quality control system to verify cement dosage and slurry consistency before use.
2. Horizontal Anchor Rod Angles
Problem Description:
Self-drilling hollow bolts are intended to be installed perpendicular to the excavation contour. However, deviations from this angle can occur, leading to potential instability and leakage, particularly at the top of the arch.
Common Causes:
- Drilling Equipment Limitations: Many drilling trolleys lack height adjustment capabilities, resulting in anchors being installed at non-vertical angles.
- Drill Rig Positioning: The drilling rig or trolley might be positioned in such a way that it forces the anchor rod to be installed horizontally rather than perpendicular.
Solutions:
- Enhanced Equipment: Invest in drilling equipment that allows for precise angle adjustments to maintain verticality.
- Proper Setup: Ensure that the drilling rig or trolley is correctly positioned and stabilized to avoid deviations from the required anchor rod angle.
- Regular Inspection: Conduct frequent inspections to verify the angle of installed bolts and correct any deviations promptly.
3. Bolt Positioning Deviations and Insufficient Hole Depth
Problem Description:
Accurate bolt positioning and hole depth are essential for the effective anchoring of self-drilling hollow bolts. Deviations from the planned positions or insufficient hole depth can undermine the structural integrity of the support system.
Common Causes:
- Inaccurate Drilling: Drilling may not follow the precise markings or fixed points, leading to deviations in bolt positioning.
- Shallow Holes: Workers may drill holes that are not deep enough, often due to a lack of technical understanding or effort.
Solutions:
- Adherence to Specifications: Ensure that all drilling operations strictly follow the specified guidelines for positioning and hole depth. Use laser-guided drilling equipment to enhance accuracy.
- Random Checks: Perform spot-checks with a frequency of no less than 10% of the total number of anchor rods to ensure compliance with depth and positioning requirements.
- Training and Supervision: Train workers thoroughly on the importance of accurate drilling and positioning, and provide supervision to enforce adherence to standards.
4. Insufficient Number of Anchor Rod Roots
Problem Description:
The number of anchor rod roots can significantly impact the overall stability of the support system. Insufficient anchor roots, whether due to deliberate shortcuts or oversight, can lead to structural weaknesses.
Common Causes:
- Intentional Shortcuts: Some contractors may intentionally reduce the number of anchor rods to cut costs or save time.
- Oversights: During busy construction phases, there may be oversight in counting the anchor rods before and after grouting.
Solutions:
- Pre- and Post-Grouting Inventory: Conduct a thorough inventory of anchor rods before grouting and verify the count after grouting and before the initial spray application.
- Strict Compliance: Enforce strict compliance with the required number of anchor rods as specified in the project design. Implement a system of checks and balances to prevent shortcuts.
5. Grouting Issues: No Grouting, False Grouting, or Insufficient Grouting
Problem Description:
Proper grouting is essential for the effective performance of self-drilling hollow bolts. Issues such as no grouting, false grouting, or insufficient grouting can severely compromise the anchor's effectiveness.
Common Causes:
- Intentional Misconduct: Some workers may intentionally block the grouted opening to avoid proper grouting, a serious form of jerry-building.
- False Grouting: The use of materials to plug the grouted opening, leading to incomplete or false grouting.
Solutions:
- Grouting Verification: Inspect grouted areas for slurry overflow around the stop plug. Utilize methods such as tapping the anchor to listen for hollow sounds that indicate incomplete grouting.
- Quality Assurance: Implement a rigorous grouting quality assurance program that includes regular inspections and random checks to ensure proper grouting.
- Training and Enforcement: Educate construction workers on the importance of proper grouting and enforce strict penalties for intentional misconduct.
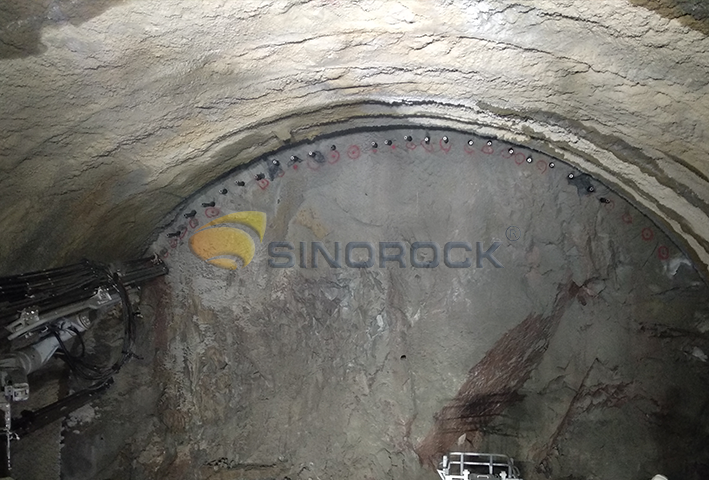
Conclusion
The construction of self-drilling hollow bolts is a sophisticated process that demands adherence to rigorous quality standards to ensure structural integrity and safety. Addressing common quality problems such as incorrect water-cement ratios, improper anchor rod angles, deviations in bolt positioning, insufficient anchor rod numbers, and grouting issues is crucial for the success of the support system. By implementing strict quality control measures, investing in advanced equipment, and adhering to best practices, construction professionals can significantly enhance the reliability and effectiveness of self-drilling hollow bolts. Ensuring high standards in these areas not only improves project outcomes but also contributes to the long-term safety and stability of the constructed structures.
latest news
-
- How to Install Self-Drilling Rock Bolts in Tunnels?
- Time:2025-07-30From:This Site
- Learn to install self-drilling rock bolts in tunnels with our step-by-step process. Ensure safe, efficient tunnel support.
- View details
-
- What Drilling Rigs Work with Self-Drilling Anchor Bolts?
- Time:2025-07-24From:This Site
- Find out which drilling rigs pair with self-drilling anchor bolts! Explore hydraulic, jumbo, and high-slope rigs for efficient tunneling and slope stabilization.
- View details
-
- Components of a Self-Drilling Anchor System
- Time:2025-07-17From:This Site
- Discover the key components of a self-drilling rock anchor system: Drill Bit, Hollow Anchor Bar, Coupler, Centralizer, Plate, and Nut. Learn their roles in geotechnical stability.
- View details
-
- Sinorock Safety Month 2025 | Everyone Speaks Safety, Everyone Can Respond
- Time:2025-07-03From:This Site
- Sinorock Safety Month 2025, centered on the theme "Everyone Speaks Safety, Everyone Can Respond - Spot Workplace Hazards," has wrapped up successfully!
- View details
-
- Quality Control: the Vital Factor of A SDA Bolt Factory
- Time:2025-01-09From:This Site
- Sinorock’s comprehensive quality control system, from supplier management to outgoing inspections, ensuring the highest standards for self-drilling anchor bolts in construction.
- View details
-
- International Women's Day with Strawberry-picking
- Time:2024-03-09From:This Site
- Marked the annual observance of International Women's Day, and to commemorate this significant event, Sinorock organized a special strawberry-picking event exclusively for its female employees.
- View details
-
- Sinorock Invites You to Explore Proven Self-Drilling Anchor Bolt Solutions at bauma 2025
- Time:2025-03-07From:This Site
- From April 7–13, 2025, explore Sinorock’s Self-drilling anchor bolt solution at Booth C2.513/4 in Hall C2 of the Messe München Exhibition Center (Munich, Germany).
- View details
-
- SINOROCK to Attend EXPOMINA PERÚ 2024 in Lima, Peru
- Time:2024-08-10From:This Site
- Sinorock to Attend EXPOMINA PERÚ 2024 in Lima, Peru
- View details
-
- SINOROCK to Participate in MINING AND METALS CENTRAL ASIA 2024
- Time:2024-08-08From:This Site
- SINOROCK to Participate in MINING AND METALS CENTRAL ASIA 2024
- View details