Anti-corrosion Mechanism
Immerse the derusted anchor bar and accessories in liquid zinc for a certain time, so that the atoms can penetrate and diffuse each other, thereby forming an iron-zinc alloy layer, which is dense, uniform, firmly bonded, bright and corrosion resistant.
Zinc is an amphoteric metal. In thermodynamics, zinc has a stable area. Hot-dip galvanizing is an electrochemical anti-corrosion method, which hinder further corrosion through insoluble chemical substances produced by interaction between zinc and concrete solution.
Product Standard
Sinorock has formulated the standard for galvanized products coatings in accordance with ISO 1461 " Hot dip galvanized coatings on fabricated iron and steel articles — Specifications and test methods". The coating thickness of main products is as follows:
Product |
Mean Coating Thickness(min.)/μm |
Local Coating Thickness(min.)/μm |
Hollow Anchor Bar |
85 |
70 |
Coupler |
55 |
45 |
Nut |
55 |
45 |
Plate |
85 |
70 |
Centralizer |
55 |
45 |
Wedge |
55 |
45 |
Note: This table is for general use, and we can also meet customers' special requiretments. |
Technical Process
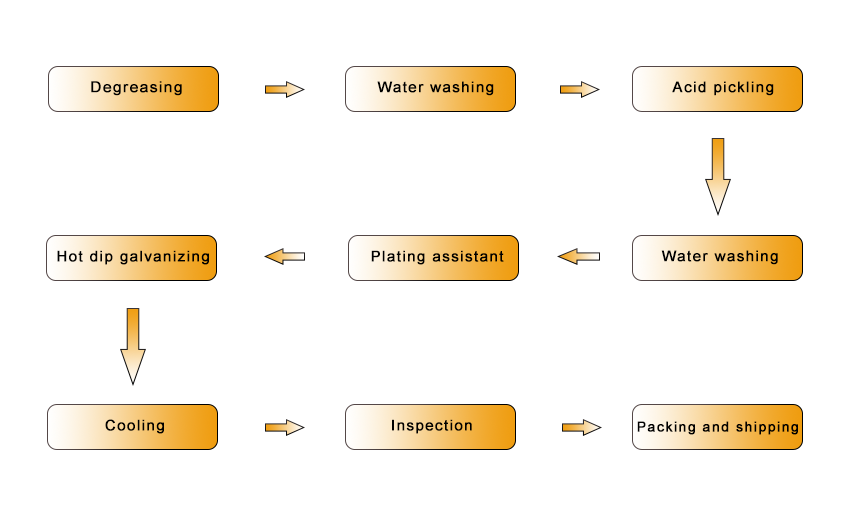
Featurs and Advantages
Excellent anti-corrosion properties: As zinc is an active metal, after coating surface is damaged, it will protect the steel by battery effect.
Long service life: Zinc layer is consumed very slowly in the atmosphere, so its service life far exceeds that of any other coatings.
Full protection: As immersed into hot-dip galvanizing bath, products are fully protected and anti-corrosion effect is better.
Lower price: In most cases, the hot-dip galvanizing cost is lower. Zinc coating is more durable than others, and does not require maintenance in the future.
High processing efficiency: Hot-dip galvanizing bath is simple and efficiency is higher than other coatings.
Not affect steel performance: Hot-dip galvanizing is carried out in an environment of more than 400 ℃, and will not affect the performance and toughness of steel.
Service Life
Generally, the service life of hot-dip galvanized products is more than 50 years in most environments, and it will be different according to corrosion level of the environment.
According to ISO 12944-2 "Paints and varnishes- Corrosion protection of steel structures by protective paint systems-Part 2: Environmental classification" (equivalent to GB/T 30790.2), The table below lists the reference rates for different atmospheric-corrosivity environment categories.
Corrosivity category |
Mass loss per unit surface/thickness loss
(after first year of exposure) |
Examples of typical environments in a temperate climate
(informative only) |
Steel |
Zinc |
Exterior |
Interior |
Mass loss(g/m2) |
Thickness Loss
(um) |
Mass Loss
(g/m2) |
Thickness Loss
(um) |
C1
very low |
≤10 |
≤1.3 |
≤0.7 |
≤0.1 |
- |
Heated buildings with clean atmospheres
e.g. offices, shops, schools, hotels |
C2
low |
>10 to 200 |
>1.3 to 25 |
>0.7 to 5 |
>0.1 to 0.7 |
Atmospheres with low level of pollution:
mostly rural areas |
Unhheated buildings where condensation can occur,
e.g. depots, sports halls |
C3
medium |
>200 to 400 |
>25 to 50 |
>5 to 15 |
>0.7 to 2.1 |
Urban and industrial atmospheres,
moderate sulfur dioxide pollution;
coastal areas with low salinity |
Production rooms with high humidity
and some air pollution
e.g. food - processing plants,
laundries, breweries, dairies |
C4
high |
>400 to 650 |
>50 to 80 |
>15 to 30 |
>2.1 to 4.2 |
Industrial areas and coastal areas
with moderate salinity |
Chemical plants, swimming pools,
coastal ships and boatyards |
C5-I
Very high
Industrial |
>650 to 1500 |
>80 to 200 |
>30 to 60 |
>4.2 to 8.4 |
Industrial and coastal areas withhigh humidity and aggressive atmosphere |
Buildings with almost constant
condensation and a high contaminated atmosphere |
C5-M
very high
Marine |
>650 to 1500 |
>80 to 200 |
>30 to 60 |
>4.2 to 8.4 |
Coastal and ocean areas
with high salinity |
Buildings with almost constant
condensation and a high contaminated atmosphere |
Note:
The highest reduction in coating thickness happens during the first year. As time goes on, the corrosion rate is greatly reduced, because the chemical substances produced by interaction between zinc and the environment hinder its further corrosion. |
Application
Hot dip galvanizing anchor bolt is especially suitable for various acid, alkali mist and other corrosive environments, as well as occasions with longer service life requirements and complex environments in geotechnical engineering.