What Is the Difference Between Casing Drilling And Self-Drilling Anchor Bolt
Time:2024-09-29From:sinorock View:
In construction, especially in geotechnical and foundation support projects, there are various methods available to secure unstable ground. Two key techniques that are often compared are casing drilling and self-drilling anchor bolt systems. Both methods are crucial in ensuring the safety and stability of projects, particularly when dealing with loose geological formations or challenging ground conditions.
In recent years, there has been a shift towards the use of self-drilling anchor bolts as an alternative to traditional casing drilling. This article will provide a detailed exploration of the differences between these two methods, highlighting the advantages and disadvantages of each and offering insights into their application in the current state of the industry.
Introduction to Casing Drilling Technology
The Basics of Casing Drilling
Casing drilling is a conventional technique that has been widely used in geotechnical construction projects. The primary purpose of casing drilling is to stabilize the borehole walls while drilling through loose or unstable formations. This method is particularly effective in preventing the collapse of the borehole, which is crucial when working in soft soils, quicksand layers, or fractured rock.
Casing drilling involves the use of a protective steel pipe, known as a casing, which is inserted into the borehole as drilling progresses. The casing serves to maintain the integrity of the borehole, preventing loose material from falling in and potentially damaging the drilling equipment or obstructing the hole.
Types of Casing Drilling Methods
There are various methods of casing drilling, and the choice of method depends on factors such as the type of drill rig, the specific construction requirements, and the formation conditions. The most commonly used methods include:
Eccentric Overburden Casing Drilling: In this method, the casing is advanced simultaneously with the drill bit, and the drill bit is slightly offset from the centerline. This allows the casing to penetrate the ground more efficiently, even in loose or fractured formations.
Symmetric Overburden Casing Drilling: This technique involves the use of a casing shoe and a symmetric drill bit, which allows the casing to be advanced while drilling. The drill bit is designed to work in tandem with the casing, ensuring that the borehole remains stable throughout the drilling process.
Each of these methods has its advantages, but both are primarily aimed at providing stability to the borehole during drilling. Casing drilling is particularly well-suited for loose strata, quicksand layers, and areas where borehole collapse is a significant risk.
Applications of Casing Drilling
Casing drilling is frequently used in environments where loose or fragmented soil is present, and the risk of borehole collapse is significant. Typical applications include:
Tunnel Construction: Casing drilling is used to stabilize loose ground during the excavation of tunnels, ensuring the safety of workers and equipment.
Slope Stabilization: In steep or unstable slopes, casing drilling provides the necessary support to prevent landslides and erosion.
Foundation Support: For high-rise buildings or structures built on unstable ground, casing drilling ensures that the foundation piles remain intact during the construction process.
Challenges and Limitations of Casing Drilling
Despite its effectiveness, casing drilling comes with several challenges:Complex Construction Process: The process of casing drilling can be complicated, requiring precise coordination between drilling and casing advancement. This increases the time and labor required for construction.
Costly: The need for casing materials and the extended time required to complete the drilling process can lead to higher overall costs.
Not Suitable for Tight Spaces: Casing drilling often requires large and specialized equipment, making it difficult to perform in confined or narrow construction spaces.
Introduction to Self-Drilling Anchor Bolt Systems
What Are Self-Drilling Anchor Bolts?
Self-drilling anchor bolts (SDAs) are an advanced drilling technology designed to address some of the limitations of traditional casing drilling. These systems are particularly effective in challenging geological conditions, such as fractured rock or soft soils, where conventional drilling methods may struggle.
A self-drilling anchor bolt consists of a hollow bar with a sacrificial drill bit at the tip. During the drilling process, the hollow bar acts both as the drill rod and the anchor, eliminating the need for a separate casing. Once drilling is complete, the hollow bar remains in the ground, providing permanent support for the structure.
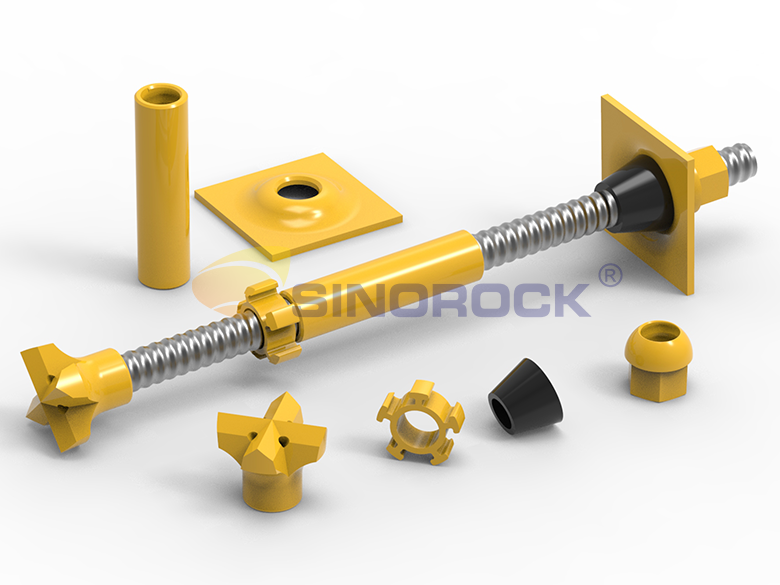
The Construction Process of Self-Drilling Anchor Bolts
Before the installation of self-drilling anchor bolts, it is essential to inspect the components, including the drill bit, hollow bar, and drill rig, to ensure they are in good working condition. The hollow bar is connected to both the drill rig and the grouting machine using a rotary grouting adapter. This adapter allows the system to perform drilling and grouting simultaneously.
The construction process follows these steps:
Drilling and Grouting: The self-drilling anchor bolt is drilled into the ground, with the hollow bar acting as both the drill string and the anchor. As drilling progresses, grout is pumped through the hollow bar, filling any voids and reinforcing the surrounding material.
Anchoring: Once drilling and grouting are complete, the anchor plate and nuts are installed at the surface, ensuring that the anchor is securely fastened and providing additional support.
Flexibility: Self-drilling anchor bolts are particularly useful in environments where traditional drilling methods may be impractical, such as in narrow or confined spaces. The flexibility of the system allows it to be used in a wide range of applications, including slope stabilization, tunnel support, and foundation reinforcement.
Advantages of Self-Drilling Anchor Bolts
Self-drilling anchor bolts offer several key advantages over traditional casing drilling:
Simplified Construction Process: The elimination of the need for a separate casing reduces the complexity of the drilling process. Drilling and grouting can be performed simultaneously, streamlining the construction process and reducing labor costs.
Improved Efficiency: By combining drilling, grouting, and anchoring into a single operation, self-drilling anchor bolts can significantly reduce the overall construction time.
Cost-Effective: The reduced labor and material requirements make self-drilling anchor bolts a more economical choice for many construction projects.
Adaptability: Self-drilling anchor bolts are highly adaptable and can be used in a wide range of geological conditions. They are particularly well-suited for difficult-to-form surrounding rock and fragmented strata.
Key Differences Between Casing Drilling and Self-Drilling Anchor Bolt Systems
While both casing drilling and self-drilling anchor bolt systems are used for ground support in construction projects, there are several fundamental differences between the two methods. These differences make self-drilling anchor bolts a more efficient and cost-effective solution in many situations.1. Efficiency and Speed of Construction
One of the most significant differences between casing drilling and self-drilling anchor bolts is the speed of construction. In casing drilling, the process is broken into several stages: drilling, casing installation, anchor placement, and grouting. Each of these steps requires time, coordination, and labor, making the overall process longer and more complex.
In contrast, self-drilling anchor bolts combine these steps into one seamless operation. The drilling, installation, and grouting are all performed simultaneously, which can dramatically reduce the time required for a project. This efficiency makes SDAs an attractive option for projects with tight deadlines or where minimizing disruption is critical.
2. Cost Comparison
Cost is a key factor in any construction project, and here, the differences between casing drilling and SDAs are stark. Casing drilling requires additional materials (such as casings) and multiple stages of labor, each contributing to the overall project cost. Furthermore, the complexity of casing drilling often necessitates specialized equipment, further increasing expenses.
On the other hand, self-drilling anchor bolts are generally more cost-effective due to their streamlined installation process. By eliminating the need for separate casings and reducing labor costs, SDAs can lower the total project budget. Additionally, SDAs can be installed in hard-to-reach areas, reducing the need for expensive site modifications or equipment.
3. Adaptability to Ground Conditions
Both methods are designed to handle challenging ground conditions, but their adaptability differs. Casing drilling is highly effective in loose or unstable soils, such as sand or gravel, where there is a high risk of the borehole collapsing during the drilling process. The casing provides a physical barrier that prevents the walls from caving in, ensuring a stable borehole for the installation of anchors.
However, self-drilling anchor bolts are specifically designed for fractured or weak rock formations and loose soils, where traditional methods might struggle. The simultaneous drilling and grouting process ensures that the surrounding ground is stabilized as the anchor is installed, reducing the risk of collapse. Additionally, SDAs can be easily lengthened with couplers to adapt to varying ground conditions.
4. Equipment Requirements
The equipment required for casing drilling is more specialized and varied. A typical casing drilling setup includes a drilling rig, casing pipes, and specialized tools for installing and removing the casing. This increases the logistical demands of the project, as more equipment and materials need to be transported to and managed on-site.
In contrast, self-drilling anchor bolts require fewer pieces of equipment. A single drilling rig equipped with a rotary grouting adapter can complete the entire process. This not only simplifies logistics but also reduces the environmental footprint of the project, as fewer resources are consumed.
5. Grouting Process
Grouting is a critical aspect of both casing drilling and self-drilling anchor bolt systems, but the timing and method of grouting differ significantly. In casing drilling, groutingoccurs after the drilling and casing processes are complete. Once the hole has been stabilized with the casing, the next step involves inserting the anchor and connecting the grouting machine to fill the voids and secure the anchor in place. This separate stage adds time and complexity to the operation.
In contrast, self-drilling anchor bolts streamline this process by allowing simultaneous drilling and grouting. As the hollow bar is drilled into the ground, grout is injected through the hollow core, filling the voids created by the drilling process. This not only stabilizes the surrounding ground but also secures the anchor in one continuous operation. The simultaneous grouting process significantly enhances the efficiency of the installation and ensures that the anchor is fully embedded within the substrate as it is being drilled.
6. Accessibility and Flexibility
When it comes to working in confined spaces or difficult-to-reach areas, self-drilling anchor bolts offer a clear advantage. Due to their compact design and the simplicity of the process, SDAs can be installed in areas where traditional casing drilling would be impractical or impossible. This includes tight urban environments, narrow underground spaces, or steep, unstable slopes where larger equipment cannot access.
Casing drilling, on the other hand, requires more space due to the need for casings and the specialized equipment involved. This makes it less suitable for confined areas or projects with limited access. Additionally, the flexibility of self-drilling anchor bolts is enhanced by the ability to easily extend the hollow bars with couplers, allowing the system to adapt to variable ground conditions and depths.
7. Environmental Impact
Construction projects today are under increasing pressure to reduce their environmental impact, and this is another area where self-drilling anchor bolts have an edge. The simplicity of the SDA system means fewer materials and resources are required for each project. The elimination of casings reduces waste, and the streamlined process results in a smaller overall footprint.
In contrast, casing drilling often involves the use of steel or plastic casings that must be transported to and from the site, adding to the environmental burden. The need for additional equipment and resources further contributes to the environmental impact, making casing drilling a less sustainable option in many cases.
8. Installation Expertise and Workforce Requirements
While both casing drilling and self-drilling anchor bolt systems require skilled labor, the level of expertise and the size of the workforce differ between the two. Casing drilling requires a larger crew to manage the various stages of the process, including drilling, casing installation, and grouting. Each stage must be carefully coordinated to ensure that the borehole remains stable and the anchors are installed correctly.
On the other hand, self-drilling anchor bolts simplify the process, requiring fewer personnel to operate the drilling rig and manage the grouting operation. While the process does require skilled technicians, the reduced number of steps means that a smaller workforce can complete the project, further lowering labor costs and improving overall efficiency.
9. Long-Term Durability and Maintenance
One of the key considerations in any geotechnical support system is the long-term durability of the installed anchors. Both casing drilling and self-drilling anchor bolts offer excellent stability, but their durability in different ground conditions can vary.
Casing drilling provides robust support in loose, sandy, or gravelly soils, where the casing helps to maintain the integrity of the borehole. However, over time, the casings themselves may be subject to corrosion or wear, especially in highly aggressive environments, necessitating periodic inspection and potential maintenance.
In contrast, self-drilling anchor bolts offer superior long-term performance in fractured rock or weak formations, where the simultaneous drilling and grouting process ensures that the anchors are fully embedded and supported by the surrounding grout. The lack of external casings means there are fewer elements exposed to potential corrosion, and the grout serves as a protective barrier, further enhancing the durability of the anchor system.
10. Project Complexity and Risk Management
Finally, the complexity and associated risks of a project must be carefully considered when choosing between casing drilling and self-drilling anchor bolts. Casing drilling is inherently more complex due to the need for multiple stages and the use of additional materials. Each stage introduces potential risks, such as casing failure, borehole collapse, or grouting issues, all of which must be carefully managed to ensure the success of the project.
In contrast, self-drilling anchor bolts offer a more straightforward, integrated solution that reduces the overall risk. By combining the drilling, anchoring, and grouting stages into one operation, there are fewer opportunities for errors or complications. This makes SDAs particularly well-suited for projects with tight deadlines or where minimizing risk is a priority.
Conclusion: Which Method is Right for Your Project?
When deciding between casing drilling and self-drilling anchor bolts, several factors must be considered, including the specific ground conditions, the project timeline, budget constraints, and the level of complexity involved.
Casing Drilling
Casing drilling remains a reliable and effective method for projects involving loose, sandy, or gravelly soils where there is a high risk of borehole collapse. It offers excellent stability and can be adapted to a wide range of geotechnical applications. However, the complexity, time requirements, and higher costs associated with casing drilling make it less suitable for projects where efficiency and budget constraints are paramount.
Casing drilling may still be the preferred choice for:
Highly unstable ground conditions where borehole collapse is a significant concern.
Large-scale projects where specialized equipment and larger workforces are available.
Projects requiring deep boreholes, such as for high-rise building foundations or large infrastructure projects.
Self-Drilling Anchor Bolts
Self-drilling anchor bolts, on the other hand, offer a modern, efficient alternative that can significantly reduce both time and costs. The ability to simultaneously drill and grout, combined with the versatility of the hollow bar system, makes SDAs an excellent choice for a wide range of geotechnical applications, particularly in fractured rock, weak formations, or confined spaces.
Self-drilling anchor bolts are particularly well-suited for:
Time-sensitive projects where minimizing the construction period is critical.
Projects in confined spaces or with limited access, such as underground mining, tunnel construction, or urban development.
Cost-conscious projects where reducing material, labor, and equipment costs is a priority.
The Role of Sinorock Self-Drilling Anchor Bolts
Sinorock, a leader in self-drilling anchor systems, provides innovative solutions tailored to the needs of modern geotechnical engineering. Sinorock's self-drilling anchor bolts are designed for use in a wide range of construction environments, including tunnel support, slope stabilization, and foundation reinforcement. Their product offerings are built to deliver maximum efficiency, durability, and cost-effectiveness, ensuring that each project is completed on time and within budget.In addition to their versatility and performance, Sinorock's self-drilling anchor bolts offer enhanced corrosion resistance, making them suitable for use in aggressive environments where long-term durability is essential. By providing an integrated drilling and grouting solution, Sinorock's systems help to minimize project complexity, reduce risks, and deliver superior outcomes.
Whether you're working on a tunnel, slope stabilization, or foundation support project, Sinorock self-drilling anchor bolts offer a proven, reliable solution that can meet the demands of even the most challenging geotechnical conditions.
Final Thoughts
In the debate between casing drilling and self-drilling anchor bolts, there is no one-size-fits-all answer. Each method has its strengths and is best suited to specific project conditions and goals. However, as the construction industry continues to evolve and prioritize efficiency, cost savings, and reduced environmental impact, self-drilling anchor bolt systems are increasingly being seen as the future of geotechnical engineering.
By understanding the unique advantages and challenges of each method, project managers and engineers can make informed decisions that ensure the success of their projects while optimizing resources and minimizing risks. Whether you choose casing drilling or self-drilling anchor bolts, the key to success lies in careful planning, proper execution, and selecting the right tools and techniques for the job.
With the continued advancements in self-drilling anchor technology, companies like Sinorock are at the forefront of providing the next generation of solutions for a wide range of construction challenges, delivering performance, reliability, and value with every installation.
latest news
-
- How to Install Self-Drilling Rock Bolts in Tunnels?
- Time:2025-07-30From:This Site
- Learn to install self-drilling rock bolts in tunnels with our step-by-step process. Ensure safe, efficient tunnel support.
- View details
-
- What Drilling Rigs Work with Self-Drilling Anchor Bolts?
- Time:2025-07-24From:This Site
- Find out which drilling rigs pair with self-drilling anchor bolts! Explore hydraulic, jumbo, and high-slope rigs for efficient tunneling and slope stabilization.
- View details
-
- Components of a Self-Drilling Anchor System
- Time:2025-07-17From:This Site
- Discover the key components of a self-drilling rock anchor system: Drill Bit, Hollow Anchor Bar, Coupler, Centralizer, Plate, and Nut. Learn their roles in geotechnical stability.
- View details
-
- Sinorock Safety Month 2025 | Everyone Speaks Safety, Everyone Can Respond
- Time:2025-07-03From:This Site
- Sinorock Safety Month 2025, centered on the theme "Everyone Speaks Safety, Everyone Can Respond - Spot Workplace Hazards," has wrapped up successfully!
- View details
-
- Quality Control: the Vital Factor of A SDA Bolt Factory
- Time:2025-01-09From:This Site
- Sinorock’s comprehensive quality control system, from supplier management to outgoing inspections, ensuring the highest standards for self-drilling anchor bolts in construction.
- View details
-
- International Women's Day with Strawberry-picking
- Time:2024-03-09From:This Site
- Marked the annual observance of International Women's Day, and to commemorate this significant event, Sinorock organized a special strawberry-picking event exclusively for its female employees.
- View details
-
- Sinorock Invites You to Explore Proven Self-Drilling Anchor Bolt Solutions at bauma 2025
- Time:2025-03-07From:This Site
- From April 7–13, 2025, explore Sinorock’s Self-drilling anchor bolt solution at Booth C2.513/4 in Hall C2 of the Messe München Exhibition Center (Munich, Germany).
- View details
-
- SINOROCK to Attend EXPOMINA PERÚ 2024 in Lima, Peru
- Time:2024-08-10From:This Site
- Sinorock to Attend EXPOMINA PERÚ 2024 in Lima, Peru
- View details
-
- SINOROCK to Participate in MINING AND METALS CENTRAL ASIA 2024
- Time:2024-08-08From:This Site
- SINOROCK to Participate in MINING AND METALS CENTRAL ASIA 2024
- View details