What Is Rock Bolting in Construction?
Time:2024-03-22From:sinorock View:
Introduction to Rock Bolting in Construction
In the realm of construction and engineering, where stability and safety are paramount, rock bolting emerges as a crucial technique. It's a method employed to fortify unstable conditions in various settings such as tunnels, slopes, mines, and foundations. Not only does rock bolting safeguard personnel and equipment, but it also ensures the longevity and durability of construction projects. This article delves into the intricacies of rock bolting, exploring its definition, types, installation procedures, advantages, applications, and maintenance protocols.Definition and Purpose of Rock Bolting
Rock bolting entails the utilization of tension members, known as bolts, to reinforce rock masses. These bolts penetrate deep into the stratum, with one end affixed to the engineering structure while the other anchors securely within the rock. The primary purpose of rock bolting is to enhance stability and mitigate the risks associated with unstable geological formations. By distributing tensile forces and prestressing the rock, this technique effectively fortifies tunnels, slopes, dams, and other structures against potential hazards like collapses and displacements.
Types of Rock Bolting Systems
Rock bolting systems come in various forms, to suit different geological conditions and construction requirements. Here are some common types:
Expandable Rock Bolts
Expandable rock bolt is also called Swellex rock bolt. It consists of end sleeves, retaining rings, liquid injection ends, trays, and other accessories. Put the steel pipe into the bolt hole and expand it with high-pressure water. During the expansion process, the expandable rock bolt is permanently deformed, the wall of the bolt is completely fitted with the irregular hole wall of the drill hole, and the rock mass is reinforced by the friction force and self-locking force generated along the entire length of the bolt.
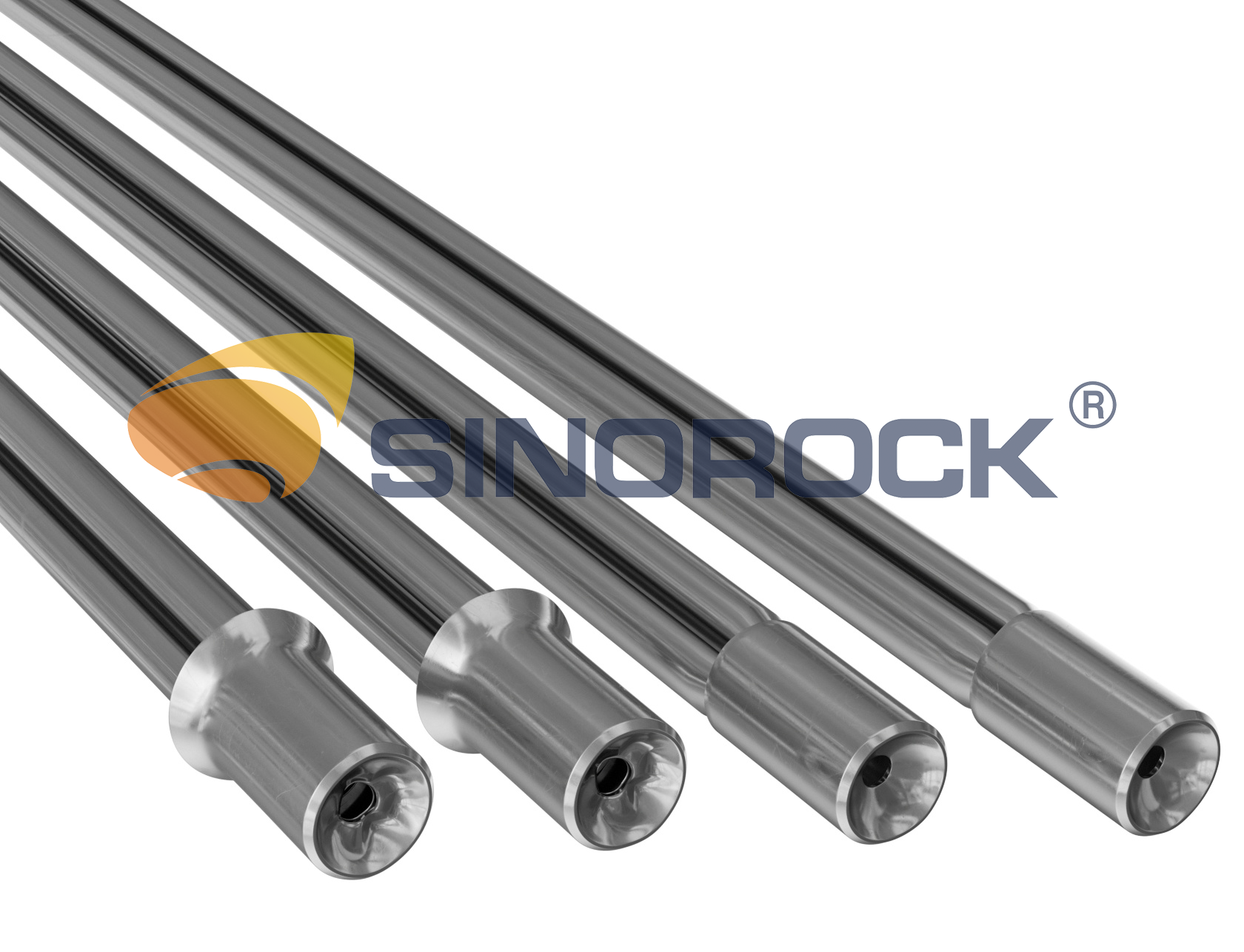
The installation procedure of expandable rock bolt involves:
1. Drilling a Hole: A hole is drilled into the rock or soil.
2. Pull out the drill rod: The drill rod which drilling before needs to be pulled out.
3. Inserting the Bolt: The Swellex rock bolt is placed into the drilled hole.
4. Expanding with Water: High-pressure water is injected to expand the bolt, ensuring a secure fit within the irregularities of the hole wall, generating friction and reinforcing the rock mass.
Expansion Shell Rock Bolt
An expansion shell rock bolt consists of an expanded shell anchor head and a hollow bolt. Usually, an expanded shell anchor head is made of high-strength steel.
The expanding shell rock bolt generates the anchoring force through the extrusion friction between the expanding shell and the inner wall of the bolt hole and can be applied to prestress to fix the hollow bolt body in the center of the anchor hole.
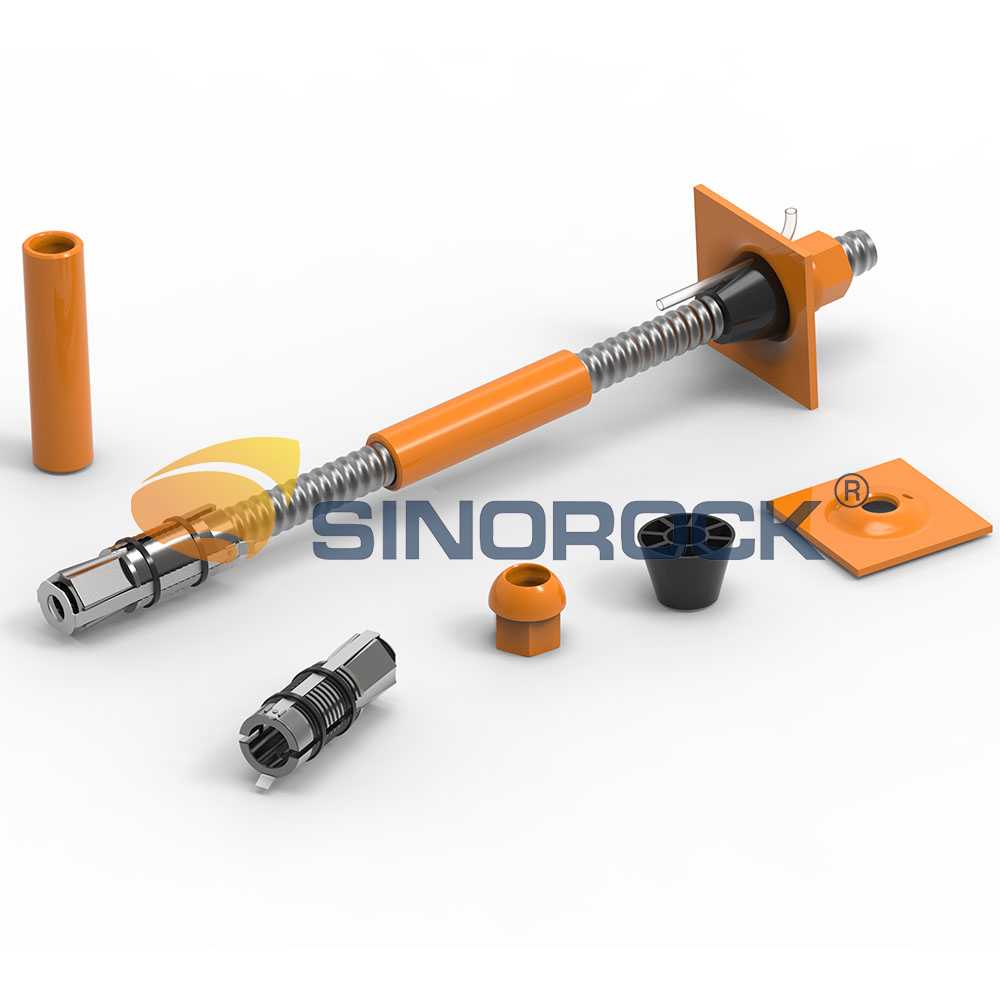
Its installation procedure includes:
1. Anchor Hole Inspection: Ventilate and inspect the anchor hole.
2. Drilling: Drill the hole to the required depth.
3. Inserting the Bolt: Place the shell bolt into the drilled hole.
4. Preloading: Apply preload to the rock rod.
5. Installation of Accessories: Install Slurry Plug, Backing Plate, and Nut.
6. Tensioning and Grouting: Apply tension and grout to reinforce the anchor.
Cable Bolts
The cable bolts are when anchored in the side holes in the suspension bridge, the main cable is divided into many strands of steel bundles and anchored respectively. These steel bundles are called cable bolts. The cable bolt is a prestressed steel strand that is fixed on the slope surface through the outer end, and the other end passes through the sliding surface of the slope and anchors in the stable rock mass under the sliding surface. The friction resistance keeps the structural surface in a compressed state to improve the integrity of the slope rock mass, thereby fundamentally improving the mechanical properties of the rock mass, effectively controlling the displacement of the rock mass, promoting its stability, and achieving the purpose of improvement of bedding and landslides and the dangerous rocks and dangerous rocks.
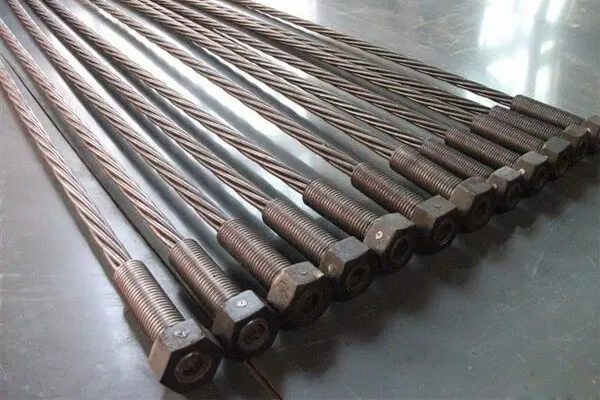
The installation procedure of cable bolts involves:
1. Drilling: Drill holes into the rock surface. During the drilling process, high-pressure water is used for flushing, and make sure there is no stagnant water, stone powder, or gravel in the hole. If the hole collapses due to the weak and broken stratum, consolidation grouting can be carried out to solidify the wall. When drilling in the loose body of the accumulation slope, to prevent the hole from collapsing, the casing should follow when drilling.
2. Fabrication: Prepare and cut the cable bolts.
3. Installation: Insert the cable bolts into the drilled holes, ensuring straightness and integrity.
4. Grouting: Grout the bolt sections sequentially to enhance reinforcement.
Self-Drilling Rock Bolts
The self-drilling rock bolt is composed of a hollow anchor bar which is divided into r thread and t thread, a sacrificial drill bit, a coupler to connect two hollow bars to extend the length, a nut, a plate, and a centralizer. It can combine drilling, grouting, and anchoring in one process. The self-drilling anchor bolt system is safe, efficient, and convenient. It is suitable for broken rock, loose soil, and geological conditions where is difficult to drill holes. It helps to ensure the anchoring effect in complex ground conditions and achieve the best construction result.
-rock-bolts.png)
The installation procedure of self-drilling rock bolt includes:
1. Confirming Drilling Position: According to the designed vertical and horizontal spacing of the bolt, the anchor rod is positioned, and the anchor rod body is directly used as the drill rod when drilling. Confirm the drilling position according to the design drawing, and then align the drill bit with the hole.
2. Cleaning: Before drilling, check whether the drilling rig and grouting machine are operating normally, and check whether the water hole of the drill bit and the interior of the bolt are unobstructed. Supply water to the anchor rod, and start drilling after the water flows out of the grouting hole of the drill bit. If there is any blockage, it should be cleaned first.
3. Drilling and Grouting: Before drilling, fix the anchor rod with the gripper, adjust the drilling rig afterward to make the drilling angle meet the design requirements, and then release the gripper. During the drilling process, the rod body and the grouting hole are washed with pressurized water or cement slurry prepared according to a certain water-cement ratio through the screw grouting machine, and the anchor rod is repeatedly rotated to ensure that there is no residual slag in the entire drilling hole. Grouting provides protection.
The screw grouting machine is used for grouting to achieve the effect of simultaneous drilling and grouting. When using pure cement slurry or 1:1 mortar, the particle size of the sand should not be greater than 1.0mm, and the water-cement ratio should be controlled at 0.4~0.5. Open the grouting valve and start grouting into the hole through the self-drilling hollow bolt, and stop grouting after the orifice returns to the grouting for about 1 minute.
4. Installing Accessories: After the grout is solidified, install the backing plate on the exposed section of the self-drilling hollow bolt close to the surface of the rock and soil body. The anchoring force of the hollow bolt body can be transferred to the backing plate by applying pre-tightening force, and the backing plate can be pressed to the rock. To prevent the deformation of the rock mass, it is fixed with the corresponding nut to transmit the pressure.
Advantages and Disadvantages of Rock Bolting
Advantages:
- Enhanced Stability: Rock bolting reinforces unstable conditions, preventing collapses and slope failures.
- Versatility: Various types of rock bolts cater to different geological and construction requirements.
- Efficiency: Self-drilling rock bolts streamline the installation process, saving time and labor costs.
- Durability: Properly installed rock bolts provide long-term structural support and stability.
Disadvantages:
- Cost: The initial investment for rock bolting equipment and materials can be significant.
- Complexity: Installation like cable anchors or other complex rock bolts may require specialized knowledge and expertise, particularly in challenging geological conditions.
- Maintenance: Regular inspection and maintenance are necessary to ensure the continued effectiveness of rock bolts.
Applications of Rock Bolting in Construction Projects
Rock bolting finds extensive applications in various construction projects, including:
- Tunneling: Reinforcing tunnel walls to prevent collapses and ensure safe passage.
- Slope Stabilization: Mitigating the risk of landslides and slope failures in infrastructure projects.
- Mining: Supporting underground excavations and preventing roof collapses.
- Foundation Reinforcement: Enhancing the stability of building foundations in areas with weak or shifting soils.
Maintenance and Inspection of Rock Bolts
Regular maintenance and inspection are essential to ensure the continued effectiveness of rock bolts. Key maintenance tasks include:
- Visual Inspection: Regularly inspect rock bolts for signs of corrosion, deformation, or damage.
- Testing: Conduct periodic load testing to assess the structural integrity of the bolts.
- Grouting: Monitor and maintain proper grouting to ensure secure anchoring and reinforcement.
- Repair and Replacement: Promptly repair or replace damaged or deteriorated rock bolts to maintain structural stability.
Conclusion
Rock bolting plays a vital role in construction by providing reinforcement and stability in challenging geological conditions. With various types of rock bolts available, construction professionals can choose the most suitable option based on project requirements and geological considerations. While rock bolting offers numerous advantages, it requires proper installation, maintenance, and inspection to ensure long-term effectiveness and structural safety. By understanding the different types of rock bolts and their installation procedures, construction teams can enhance safety, mitigate risks, and ensure the success of their projects.
latest news
-
- How to Install Self-Drilling Rock Bolts in Tunnels?
- Time:2025-07-30From:This Site
- Learn to install self-drilling rock bolts in tunnels with our step-by-step process. Ensure safe, efficient tunnel support.
- View details
-
- What Drilling Rigs Work with Self-Drilling Anchor Bolts?
- Time:2025-07-24From:This Site
- Find out which drilling rigs pair with self-drilling anchor bolts! Explore hydraulic, jumbo, and high-slope rigs for efficient tunneling and slope stabilization.
- View details
-
- Components of a Self-Drilling Anchor System
- Time:2025-07-17From:This Site
- Discover the key components of a self-drilling rock anchor system: Drill Bit, Hollow Anchor Bar, Coupler, Centralizer, Plate, and Nut. Learn their roles in geotechnical stability.
- View details
-
- Sinorock Safety Month 2025 | Everyone Speaks Safety, Everyone Can Respond
- Time:2025-07-03From:This Site
- Sinorock Safety Month 2025, centered on the theme "Everyone Speaks Safety, Everyone Can Respond - Spot Workplace Hazards," has wrapped up successfully!
- View details
-
- Quality Control: the Vital Factor of A SDA Bolt Factory
- Time:2025-01-09From:This Site
- Sinorock’s comprehensive quality control system, from supplier management to outgoing inspections, ensuring the highest standards for self-drilling anchor bolts in construction.
- View details
-
- International Women's Day with Strawberry-picking
- Time:2024-03-09From:This Site
- Marked the annual observance of International Women's Day, and to commemorate this significant event, Sinorock organized a special strawberry-picking event exclusively for its female employees.
- View details
-
- Sinorock Invites You to Explore Proven Self-Drilling Anchor Bolt Solutions at bauma 2025
- Time:2025-03-07From:This Site
- From April 7–13, 2025, explore Sinorock’s Self-drilling anchor bolt solution at Booth C2.513/4 in Hall C2 of the Messe München Exhibition Center (Munich, Germany).
- View details
-
- SINOROCK to Attend EXPOMINA PERÚ 2024 in Lima, Peru
- Time:2024-08-10From:This Site
- Sinorock to Attend EXPOMINA PERÚ 2024 in Lima, Peru
- View details
-
- SINOROCK to Participate in MINING AND METALS CENTRAL ASIA 2024
- Time:2024-08-08From:This Site
- SINOROCK to Participate in MINING AND METALS CENTRAL ASIA 2024
- View details