Corrosion-Resistant Power: Hot-Dip Galvanized Self-Drilling Anchor Bolts
Time:2023-07-13From:sinorock View:
Hot-dip galvanized self-drilling anchor bolts play a crucial role in various construction projects, providing a reliable and robust anchoring solution. These bolts are designed to resist corrosion and offer enhanced durability, making them suitable for a wide range of applications. Understanding the principle of corrosion protection, the anti-corrosion characteristics, and the suitable application scenarios for hot-dip galvanized self-drilling anchor bolts is crucial to ensure their optimal performance.Principle of Corrosion Protection for Hot-Dip Galvanized Self-Drilling Anchor Bolts
Hot-dip galvanizing is a widely adopted method for achieving effective corrosion resistance. The process involves immersing the anchor bolts in a molten zinc bath, forming a metallurgical bond between the zinc coating and the steel substrate.
During hot-dip galvanizing, the zinc coating serves as a sacrificial barrier, shielding the underlying steel from corrosive elements such as moisture, oxygen, and chemicals. If the steel is exposed due to damage or wear, the zinc sacrificially corrodes instead, providing continuous protection. This galvanic protection mechanism ensures that the anchor bolts remain corrosion-free, even in aggressive environments.
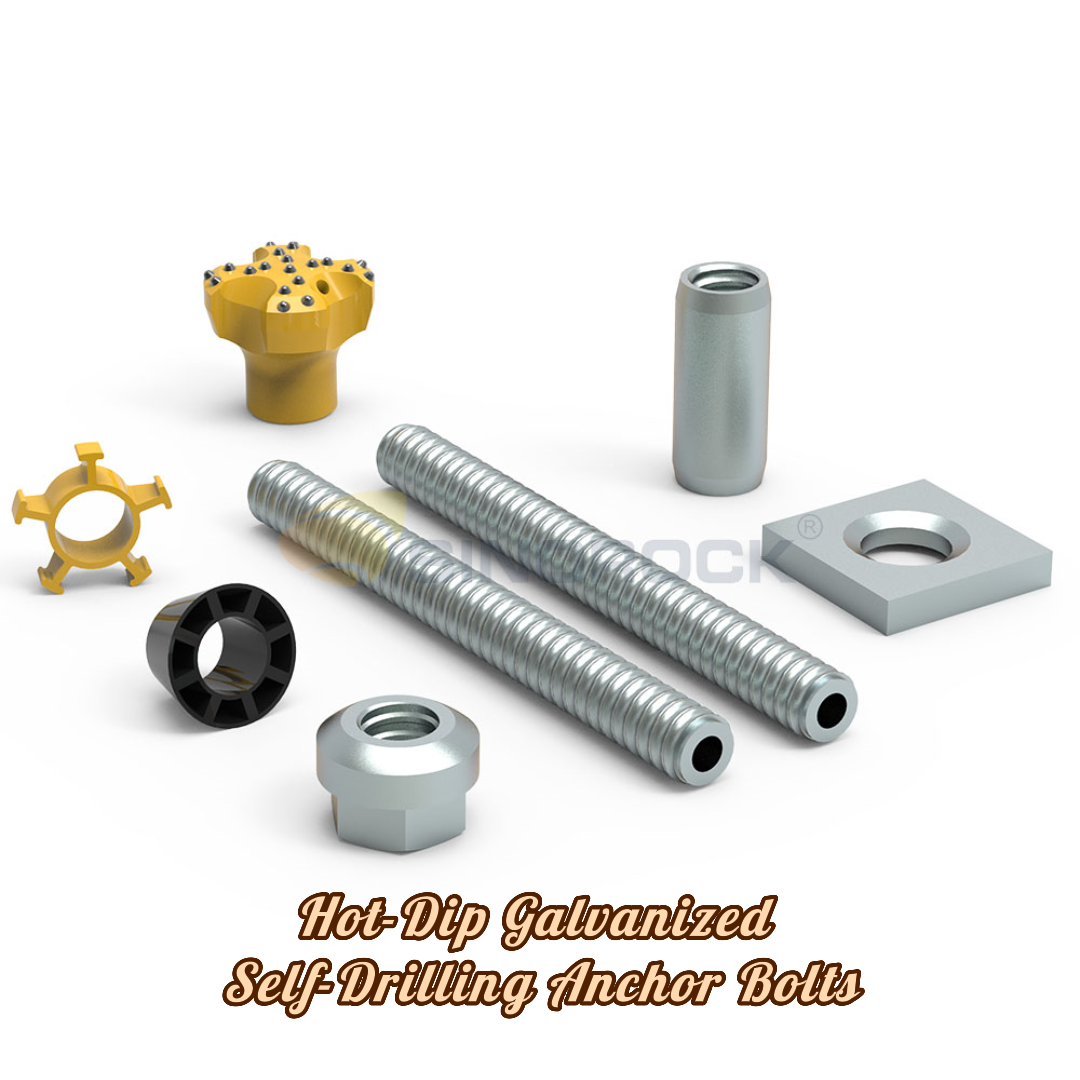
Anti-Corrosion Characteristics of Hot-Dip Galvanized Self-Drilling Anchor Bolts
1. Enhanced Durability:
Hot-dip galvanized self-drilling anchor bolts offer exceptional durability due to their corrosion-resistant properties. The thick, uniform zinc coating provides a robust barrier against rust and corrosion, extending the service life of the bolts. Moreover, the zinc layer is consumed very slowly in the atmosphere and its life span far exceeds that of any other coating.
2. Self-Healing:
In the event of minor coating damage, the zinc layer on hot-dip galvanized self-drilling anchor bolts has the ability to self-heal. The zinc will naturally react with moisture and carbon dioxide in the atmosphere, forming a protective layer of zinc carbonate. This self-healing property helps maintain the integrity of the coating and prevents further corrosion.
3. Complete Coverage:
The process of hot-dip galvanizing is zinc bath corrosion protection, which ensures that the entire surface of the self-drilling anchor bolts, including recesses, threads, and crevices, is thoroughly protected. This complete coverage provides superior corrosion resistance, even in hard-to-reach areas.
4. Inexpensive:
In most cases, hot-dip galvanizing is less expensive and more durable than other paint coatings, and requires no maintenance at a later date.
5. Short Production Cycle:
The hot-dip galvanizing process involves subjecting the product to a zinc bath, a simple process that allows for faster processing efficiency compared to other coatings.
6. Steel Performance is Not Affected:
The hot-dip galvanizing treatment is carried out at over 400°C and does not affect the performance or toughness of the steel.
7. Efficient Construction:
The self-drilling feature of these anchor bolts eliminates the need for pre-drilling, making them efficient and cost-effective for installation in various materials, including concrete, masonry, and wood.
Application Scenarios for Hot-Dip Galvanized Self-Drilling Anchor Bolts
1. Infrastructure Projects:
Hot-dip galvanized self-drilling anchor bolts find extensive use in infrastructure projects such as bridges, highways, and tunnels. These projects often involve exposure to harsh weather conditions and corrosive environments. The corrosion resistance of galvanized anchor bolts ensures their long-term performance and minimizes maintenance requirements.
2. Marine and Coastal Structures:
In marine environments, self-drilling anchor bolts are subjected to the corrosive effects of saltwater, humidity, and airborne salts. The hot-dip galvanized coating provides excellent protection against these corrosive elements, making the bolts well-suited for applications such as seawalls, piers, and offshore structures.
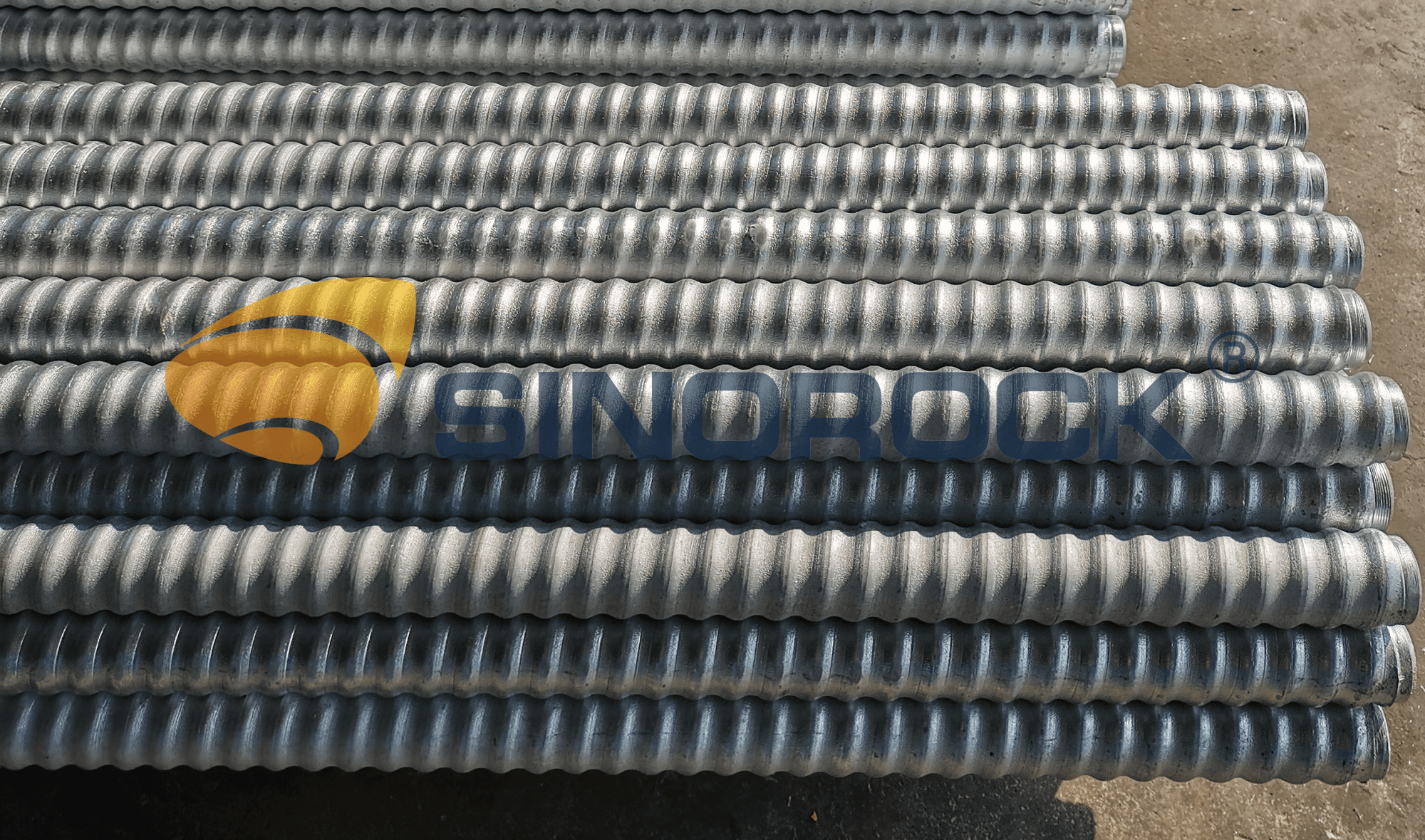
3. Industrial Facilities:
Industrial environments often expose anchor bolts to chemicals, pollutants, and moisture, leading to accelerated corrosion. Hot-dip galvanized self-drilling anchor bolts are resistant to a wide range of corrosive substances commonly found in industrial settings. They are commonly used in power plants, factories, and chemical processing plants.
4. Construction in High Humidity Areas:
In regions with high humidity or heavy rainfall, corrosion can be a significant concern for anchor bolts. Hot-dip galvanized self-drilling anchor bolts provide reliable protection against moisture-induced corrosion, making them ideal for applications in such areas.
Conclusion
Hot-dip galvanized self-drilling anchor bolts offer a robust and corrosion-resistant solution for various construction applications. Their corrosion resistance makes them reliable and cost-effective options, minimizing maintenance requirements and ensuring the structural integrity of various applications.
When considering anchor bolts for a project, engineers should evaluate the specific environmental conditions, potential exposure to corrosive elements, and the expected service life. By selecting hot-dip galvanized self-drilling anchor bolts, engineers can ensure the longevity and performance of their structures, enhancing safety and minimizing long-term maintenance costs.
As a professional manufacturer of anti-corrosion self drilling rock bolts,Sinorock provides different types of corrosion protection to suit different application environments. If you want to know more about anti-corrosion rock bolts, please contact sinorock@sinorockco.com for product information.
latest news
-
- What Are the Applications of SDA Bolts in Hydropower Stations?
- Time:2025-08-21From:This Site
- Learn how self-drilling anchor bolts enhance slope stability, tunnel support, and dam reinforcement in complex geological conditions at hydropower stations. Optimize hydropower projects with efficient, cost-effective, and eco-friendly solutions.
- View details
-
- Slope Stabilization with SDA Bolts: Benefits & Applications
- Time:2025-08-19From:This Site
- Discover how self-drilling anchor bolts (SDA bolts) provide superior slope stabilization for highways, railways, and tunnels. Learn their key benefits, installation process, and real-world applications in loose or collapsible soils.
- View details
-
- How Self-Drilling Rock Bolts Enhance Tunnel Support in Fractured Rock?
- Time:2025-08-15From:This Site
- Discover how self-drilling rock bolts enhance tunnel support in fractured rock. Learn their benefits, installation steps, and real-world applications for safe, efficient tunneling.
- View details
-
- Sinorock 2025 Quality Month | Strengthening Quality Foundations, Empowering Product Excellence
- Time:2025-08-13From:This Site
- Sinorock’s 2025 Quality Month, themed “Strengthening Quality Foundations, Empowering Product Excellence,” successfully concluded, reinforcing our commitment to superior product quality.
- View details
-
- Sinorock Safety Month 2025 | Everyone Speaks Safety, Everyone Can Respond
- Time:2025-07-03From:This Site
- Sinorock Safety Month 2025, centered on the theme "Everyone Speaks Safety, Everyone Can Respond - Spot Workplace Hazards," has wrapped up successfully!
- View details
-
- Quality Control: the Vital Factor of A SDA Bolt Factory
- Time:2025-01-09From:This Site
- Sinorock’s comprehensive quality control system, from supplier management to outgoing inspections, ensuring the highest standards for self-drilling anchor bolts in construction.
- View details
-
- Sinorock Invites You to Explore Proven Self-Drilling Anchor Bolt Solutions at bauma 2025
- Time:2025-03-07From:This Site
- From April 7–13, 2025, explore Sinorock’s Self-drilling anchor bolt solution at Booth C2.513/4 in Hall C2 of the Messe München Exhibition Center (Munich, Germany).
- View details
-
- SINOROCK to Attend EXPOMINA PERÚ 2024 in Lima, Peru
- Time:2024-08-10From:This Site
- Sinorock to Attend EXPOMINA PERÚ 2024 in Lima, Peru
- View details
-
- SINOROCK to Participate in MINING AND METALS CENTRAL ASIA 2024
- Time:2024-08-08From:This Site
- SINOROCK to Participate in MINING AND METALS CENTRAL ASIA 2024
- View details