Hollow Grouting Anchor Bars in Tunnels: Unveiling Neglected Quality Concerns
Time:2024-07-24From:sinorock View:
Tunnel construction is a field where precision and reliability are paramount. Among the critical elements that ensure the stability and safety of tunnels are self-drilling hollow grouting anchor bars. These components are vital not only for supporting the rock during excavation but also for providing enduring stability in the completed structure. Despite their importance, numerous quality concerns often compromise their effectiveness. This article delves into these issues, offering solutions and insights to enhance the reliability of hollow grouting anchor bars in tunnel construction.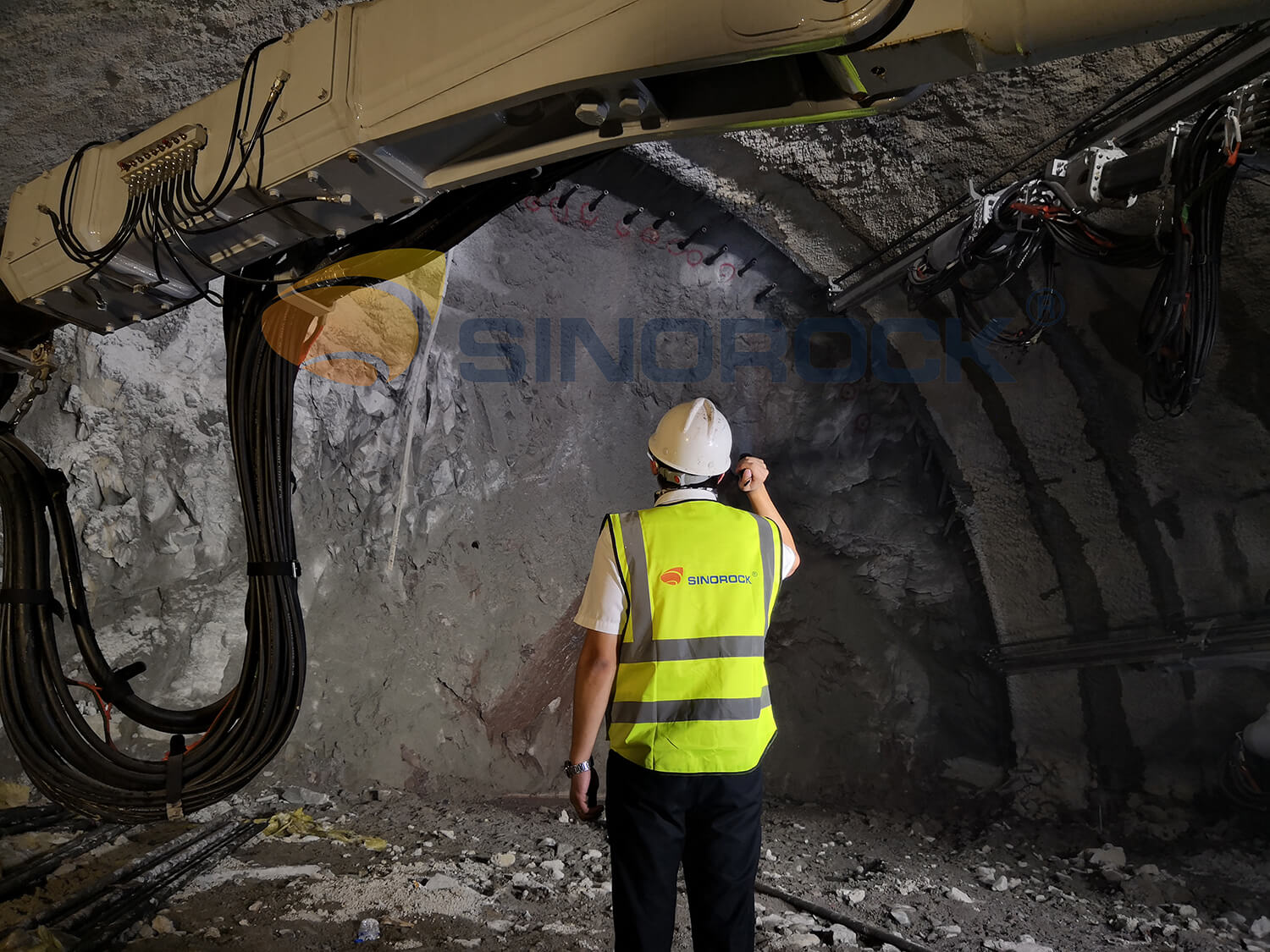
Common Quality Problems and Their Solutions
1. Incorrect Mix Ratio and Insufficient Cement
One of the most fundamental issues in the use of hollow grouting anchor bars is the incorrect mix ratio of the grout or insufficient cement content. The effectiveness of an anchor bar is heavily reliant on the quality of the grout used. An improper mix ratio can lead to inadequate bonding between the anchor bar and the rock, significantly reducing the support strength.
Solution:
To mitigate this problem, it is essential to adhere strictly to the recommended mix ratios and ensure that the cement content is adequate. Implementing stringent quality control measures, including regular checks of the mix proportions, is crucial. Using automated mixing systems and digital controls can help maintain consistency and accuracy in grout preparation.
2. Anchor Bar Installation Angle is Horizontal
The angle at which anchor bars are installed is critical for their effectiveness. A common issue is the installation of anchor bars at a horizontal angle rather than the recommended angle. This often occurs due to limitations in the drilling equipment or errors in alignment, particularly when using a drilling jumbo that cannot be adjusted vertically.
Solution:
To address this issue, it is important to provide comprehensive training to personnel involved in the installation process. Ensuring that drill operators and installation teams understand the importance of maintaining the correct angle will enhance the overall effectiveness of the anchor bars. Additionally, investing in adjustable drilling equipment can help achieve the desired installation angles more consistently.
3. Deviation in Anchor Bar Positioning and Insufficient Hole Depth
Accurate positioning and proper hole depth are essential for the effective performance of anchor bars. Deviations in positioning or insufficient hole depth can significantly reduce the support provided by the anchor bars. These issues often stem from poor adherence to technical guidelines or attempts to expedite the construction process.
Solution:
Incorporating advanced positioning technologies, such as GPS-based systems, can help ensure precise placement of anchor bars. Regular quality checks and adherence to drilling specifications are also crucial. Using automated drilling systems that provide real-time feedback on hole depth and positioning can further enhance accuracy.
4. Insufficient Number of Anchor Bars
Using fewer anchor bars than recommended can compromise the structural stability of the tunnel. This practice is often driven by attempts to cut costs or save time, but it undermines the safety of the entire project.
Solution:
Strict adherence to the engineering design specifications is necessary to ensure the correct number of anchor bars is used. Site managers should be well-versed in design drawings and should conduct thorough counts of anchor bars before and after grouting. Implementing a robust quality assurance process that includes regular audits can help prevent shortcuts and ensure compliance with safety standards.
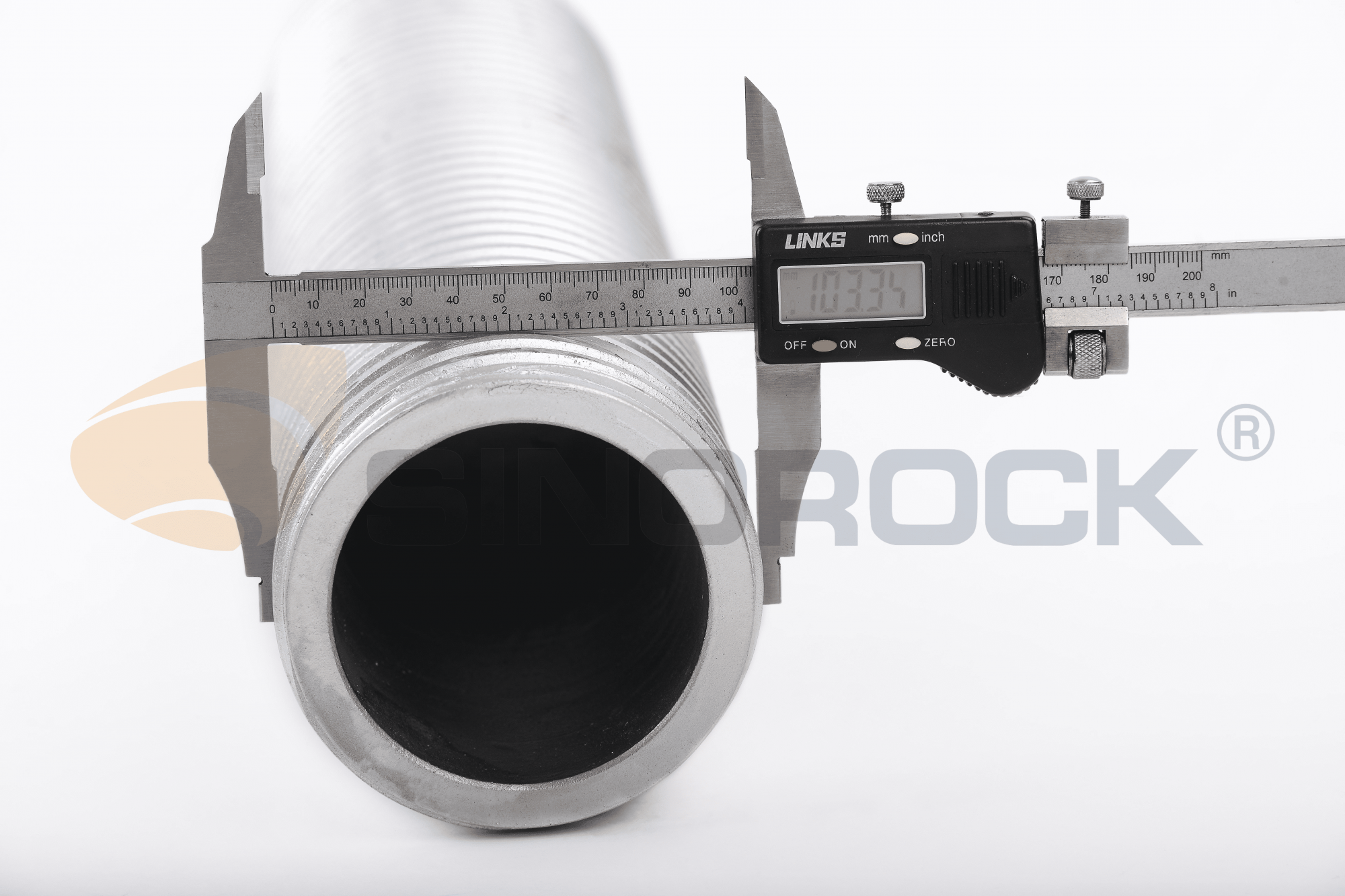
5. Grouting Issues: None, False, or Insufficient
Proper grouting is essential for creating a secure bond between the anchor bar and the rock. Issues such as lack of grouting, false grouting, or insufficient grout density can lead to catastrophic failures. Problems may arise from issues like an improperly sealed stopper plug or insufficient pressure during grouting.
Solution:
Meticulous monitoring of the grouting process is essential. Each step, from mixing to application, should be carefully overseen to ensure that the grout is applied correctly and reaches the required density. Using advanced grouting equipment and techniques, such as pressure monitoring and real-time grouting assessments, can help address these issues effectively.
Quality Control and Management Strategies
1. Staffing
Effective construction requires a well-organized team. Assigning a minimum of two construction workers and one tester per hole ensures that all aspects of the installation process are monitored. This team should oversee positioning, drilling angles, inter-row spacing, drilling depth, anchor insertion, and grouting.
2. Inspection of Raw Materials
Ensuring the quality of raw materials is fundamental. Materials should be registered upon arrival, inspected, and labeled. Continuous tracking and sampling of materials help maintain quality standards and accountability throughout the construction process.
3. On-Site Testing Equipment
Equipping site managers with appropriate testing tools is essential for accurate inspections. Tools such as digital cameras, rechargeable searchlights, and other advanced equipment can enhance the efficiency and precision of quality checks.
4. Whole-Process Checking
Regular inspections at every stage of the construction process are crucial for identifying and rectifying deviations before they escalate. Implementing a whole-process checking system helps ensure that quality issues are addressed promptly and effectively.
Safety Requirements
1. Regular and Irregular Checks
Frequent inspections of hollow anchor bars are necessary, especially in challenging geological conditions. Specialized personnel should conduct these inspections during each shift to ensure ongoing safety and stability.
2. Suspended Work Safety
When work is suspended, it is important to ensure that proper support systems are in place against the excavation face. Using spray concrete to close off the excavation minimizes potential hazards and maintains stability.
3. Secure Anchor Bar Construction Dollies
Proper placement and securing of construction dollies are vital to prevent accidents. Ensuring that these dollies are stable and correctly positioned reduces the risk of mishaps during construction.
4. Addressing Blockages or Bursts
In the event of issues such as wind, water, or material pipeline blockages, it is essential to halt the affected systems sequentially to manage the situation effectively and maintain safety.
5. Deformation and Cracking Remedies
Consistent monitoring of the anchor support system is necessary to detect and address deformation or cracks. Prompt action, including evacuation from danger zones if necessary, helps ensure the safety of personnel and the stability of the tunnel.
6. Reinforcement for Critical Situations
In cases of significant deformation or failure of anchor bars, installing reinforcement hollow anchor bars with lengths exceeding 1.5 times the original anchor bar is crucial. This additional support helps stabilize the tunnel and prevent further issues.
Conclusion
Tunnel construction is a demanding field where precision and reliability are crucial. Self-drilling hollow grouting anchor bars play a vital role in maintaining structural integrity and ensuring safety. By addressing common quality concerns and implementing robust quality control and management strategies, the effectiveness of these anchor bars can be significantly enhanced. The focus on rigorous quality assurance, advanced technologies, and comprehensive safety measures is essential for successful tunneling projects.
Sinorock, with its extensive experience in manufacturing self-drilling anchor bolts, stands out as a leading provider in the industry. Our commitment to quality and innovation ensures that our products meet the highest standards of performance and reliability. For inquiries about ground support solutions and to learn more about Sinorock’s offerings, please contact us at sinorock@sinorockco.com.
latest news
-
- How to Install Self-Drilling Rock Bolts in Tunnels?
- Time:2025-07-30From:This Site
- Learn to install self-drilling rock bolts in tunnels with our step-by-step process. Ensure safe, efficient tunnel support.
- View details
-
- What Drilling Rigs Work with Self-Drilling Anchor Bolts?
- Time:2025-07-24From:This Site
- Find out which drilling rigs pair with self-drilling anchor bolts! Explore hydraulic, jumbo, and high-slope rigs for efficient tunneling and slope stabilization.
- View details
-
- Components of a Self-Drilling Anchor System
- Time:2025-07-17From:This Site
- Discover the key components of a self-drilling rock anchor system: Drill Bit, Hollow Anchor Bar, Coupler, Centralizer, Plate, and Nut. Learn their roles in geotechnical stability.
- View details
-
- Sinorock Safety Month 2025 | Everyone Speaks Safety, Everyone Can Respond
- Time:2025-07-03From:This Site
- Sinorock Safety Month 2025, centered on the theme "Everyone Speaks Safety, Everyone Can Respond - Spot Workplace Hazards," has wrapped up successfully!
- View details
-
- Quality Control: the Vital Factor of A SDA Bolt Factory
- Time:2025-01-09From:This Site
- Sinorock’s comprehensive quality control system, from supplier management to outgoing inspections, ensuring the highest standards for self-drilling anchor bolts in construction.
- View details
-
- International Women's Day with Strawberry-picking
- Time:2024-03-09From:This Site
- Marked the annual observance of International Women's Day, and to commemorate this significant event, Sinorock organized a special strawberry-picking event exclusively for its female employees.
- View details
-
- Sinorock Invites You to Explore Proven Self-Drilling Anchor Bolt Solutions at bauma 2025
- Time:2025-03-07From:This Site
- From April 7–13, 2025, explore Sinorock’s Self-drilling anchor bolt solution at Booth C2.513/4 in Hall C2 of the Messe München Exhibition Center (Munich, Germany).
- View details
-
- SINOROCK to Attend EXPOMINA PERÚ 2024 in Lima, Peru
- Time:2024-08-10From:This Site
- Sinorock to Attend EXPOMINA PERÚ 2024 in Lima, Peru
- View details
-
- SINOROCK to Participate in MINING AND METALS CENTRAL ASIA 2024
- Time:2024-08-08From:This Site
- SINOROCK to Participate in MINING AND METALS CENTRAL ASIA 2024
- View details