Xingyi Normal University for Nationalities Retaining Wall Reinforcement
Time:2023-09-21View:
Project Background
In the picturesque town of Dingxiao, nestled within the heart of Xingyi City, lies Xingyi Normal University for Nationalities. A place of learning and inspiration for many, this institution boasts a striking campus landscape. Among the topographical features of the campus are two significant slopes. The upper slope houses the teachers' dormitories, while the lower slope is earmarked for a proposed teaching building. The critical issue that led us to intervene in this project was the perilous condition of the retaining wall constructed in 2013.
The 11-meter high retaining wall, initially built with mortar-masonry, had deteriorated over time and was teetering on the brink of collapse. A comprehensive assessment revealed the urgent need for reinforcement and repair. However, executing this task posed formidable challenges. The primary challenge was the height of the slope, towering at 11 meters, and the need for a 9-meter wide road on top.
The original plan to utilize φ25 reinforcement bars in this project had to be altered due to equipment restrictions and unstable ground conditions. Consequently, after careful consideration, the R32 self-drilling anchor system from Sinorock was selected as the most suitable option to ensure a secure and efficient solution for this project.
Project Overview
Project Duration: | September 2020 – October 2020 |
Service Scope: | Anchoring materials, anchoring rigs, and on-site technical services |
Application: | Reinforcement and repair of retaining wall of building slope |
Application Structure: | Self-drilling anchor bars used as permanent soil nails |
Quantity Consumption: | Approximately 3000 meters of self-drilling anchor bars |
Geological Conditions: | The slope featured a composition of plain fill, red clay, strongly weathered dolomite, and moderately weathered dolomite. The top of the slope consisted of a gentle slope with a soil layer, transitioning into a rocky slope further down. The proposed site also exhibited structured dissolution slow slope landform characteristics. |
Questions and Challenge
Design Conundrum: Given the complex geological conditions, the project's designer initially proposed a reinforcement plan involving anti-slide piles and anchor support. The plan included the installation of three rows of steel pipe anti-slide piles at the foot of the slope, reinforced anchors on the slope for additional support, and the subsequent placement of steel meshes with concrete spraying. However, during the construction phase, a formidable challenge emerged. Drilling through the fill layer behind the retaining wall proved to be exceedingly difficult, despite numerous attempts, leading to project suspension.
Solutions
Faced with this impasse, our technical team quickly came up with a breakthrough solution adopted by the construction team - using R32 self-drilling anchor bars as soil nails, each with a length of 1.5 meters. These anchor bars were equipped with ESSF R32/76 drill bits, capable of drilling to a depth of 9 meters. During construction, the self-drilling anchor bar was drilled through the 4-meter retaining wall first, then penetrating the 5-meter fill layer and ultimately anchoring into the bedrock.
To facilitate this, a special adapter coupling was designed by our technical team to connect the anchor rod and drill bit to the pneumatic DTH drilling rig. This adaptation allowed for precise drilling and ensured the effectiveness of the self-drilling anchor system. Additionally, grouting was performed simultaneously with drilling, enhancing the quality of the surrounding soil and bolstering the anchoring force.
The self-drilling anchor system utilized a range of components, including a hollow anchor bar, coupler, centralizer, drill bit, plate, and nut. This comprehensive system seamlessly combined drilling, grouting, and anchoring functions into one cohesive process, with the anchor bar serving as both a drill rod and reinforcement body.
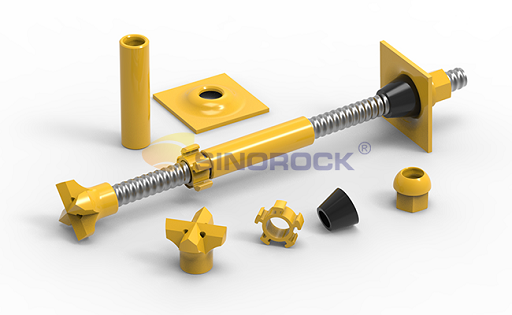
Construction Process
Materials prepared → Erect scaffolding → Drilling rig in place → Connect hollow anchor bar and drill bit → Percussive rotary drilling → Couple next anchor bar → Repeated drilling and grouting → Drilling completion → Install next row anchor bar → Installation completion
Construction Equipment
Drilling Rig
The electric DTH drilling machine JVD-100, equipped with a QCZJ90 impactor, played a pivotal role in executing the drilling tasks with precision and efficiency.
Construction Efficiency
The construction efficiency achieved during this project was nothing short of remarkable. With an average net drilling time of just 25.6 minutes per hole, even at a substantial depth of 9 meters. Each drilling rig completed over 50 meters of drilling per shift, spanning eight hours of continuous work. This efficiency was a testament to the effectiveness of Sinorock's self-drilling anchor system in addressing the complex challenges presented by the project.
Conclusion
The Xingyi Normal University for Nationalities Retaining Wall Reinforcement project stands as a testament to the capabilities and effectiveness of Sinorock's self-drilling anchor system in addressing even the most challenging slope stabilization tasks. By adopting innovative techniques and state-of-the-art equipment, this project not only ensured the safety and stability of the campus but also served as an inspiring example of engineering excellence in action. As we continue to push the boundaries of what is possible in slope stabilization, Sinorock remains committed to providing innovative solutions that safeguard lives and infrastructure, one project at a time.
latest cases
-
- The Application of Self Drilling Anchor Bolt at the Tala Hydro Project for Tunneling in Poor Rock Mass Conditions
- Time:2024-07-30From:This Site
- The Tala hydroelectric project is located in Chukha Dzongkhag in western Bhutan. The dam site is in the Thimphu gneiss, and the section of HRT up to 14km downstream from C-1 is in gneiss with quartzite bands and biotite schists. There are joint sets, and the rock is highly faulted, with foliation shears of varying thickness up to 30cm. From 14km to 23km, the rock type is biotite gneiss with bands of quartzite, mica schist, and sericite-schist with amphibolite. Rock conditions merit 3 - 4 on the NGI Q system, with pretty poor conditions affecting parts of C2, C-3 and all of C-4. The rock format
- View details
-
- Pre-support with Pipe Umbrella System for Gaojiaping Tunnel
- Time:2022-08-04From:This Site
- The success of the Gaojiaping Tunnel's construction demonstrates the ingenuity of Sinorock's self-drilling anchor system. It not only overcame the geological challenges but also enhanced safety and efficiency in tunnel construction. As China's infrastructure projects continue to push boundaries, Sinorock's commitment to professionalism and reliable products ensures a safer and more efficient future.
- View details
-
- The Construction Method of Self Drilling Anchor Bolt in Sandy Gravel Deep Excavation
- Time:2015-10-22From:This Site
- With the exploitation of the underground space in cities and the large scale construction of the underground retail spaces, the deep excavation projects is becoming more and more.
- View details
-
- Foundation Support for Hongji Group's High-end Packaging Materials Project
- Time:2023-10-20From:This Site
- Hongji Group's High-end Packaging Materials Project in Linqing City, Shandong Province, serves as a vivid example of how Sinorock's representative R32 self-drilling hollow helical anchor bolts played an instrumental role in supporting the foundation of a high-stakes industrial endeavor.
- View details
-
- Binjiang West Road Pedestrian Mall Project
- Time:2022-07-15From:This Site
- The project requires a shorter construction period and lower cost. After multiple rounds of plan review, the project party finally decided to adopt a self-drilling anchor system, using simultaneous drilling and grouting construction processes.
- View details
-
- The Application of Self Drilling Anchor Bolt in Beijing Oriental Plaza Foundation Support Project
- Time:2015-08-20From:This Site
- In the realm of modern construction and engineering, the utilization of cutting-edge technologies and innovative methodologies is paramount to overcoming the challenges posed by complex geological conditions and formidable project scopes. A prime testament to this is the remarkable application of a self-drilling anchor system in the monumental Beijing Oriental Plaza Foundation Support Project.
- View details
-
- Enhancing Slope Stabilization at the Left Bank of Xiluodu Hydropower Station with Self-Drilling Anchor Bolts
- Time:2024-10-18From:This Site
- Slope stabilization in challenging geological conditions has always been a daunting task for engineers and construction experts. In the case of the Left Bank of Xiluodu Hydropower Station, where complex geological stratifications and a short construction period posed significant challenges, the innovative application of self-drilling anchor bolts emerged as a game-changer.
- View details
-
- Xingyi Normal University for Nationalities Retaining Wall Reinforcement
- Time:2023-09-21From:This Site
- The Xingyi Normal University for Nationalities Retaining Wall Reinforcement project stands as a testament to the capabilities and effectiveness of Sinorock's self-drilling anchor system in addressing even the most challenging slope stabilization tasks.
- View details
-
- The Slope Support Project of Dong Miao Residential Area in Ji Nan
- Time:2015-10-30From:This Site
- In the ever-growing urban landscape, the challenge of stabilizing slopes and ensuring the safety of residents is of paramount importance. The success story of the Slope Support Project in the Dong Miao Residential Area, situated in the heart of Ji Nan, serves as a beacon of innovation and engineering excellence. The application of the cutting-edge Self-Drilling Anchor Bolt System has not only ensured the stability of the slopes but has also set a new standard in slope stabilization.
- View details